金属製の部品がある時間経過後に突然破壊する現象として「遅れ破壊」が知られています。
遅れ破壊は高強度鋼で起こりやすく、過去には高力ボルトで多発した事例があります。
昨今、部材軽量化などの観点から機械や構造物に高強度鋼を使用するケースが増えています。大きな事故を発生させないために、エンジニアは遅れ破壊について知識を持っておくことが大切です。
本記事では、遅れ破壊のメカニズムや対策方法などについて詳しく解説しています。ぜひ遅れ破壊について知識を取り入れていってください!
- 遅れ破壊とはどのような現象のことか
- 遅れ破壊の原因とメカニズム
- 遅れ破壊の対策
この記事は、現役の材料エンジニアが書いています!
この本を参考にしています↓↓
遅れ破壊とは?
遅れ破壊とは、材料や部品がある時間経過後に突然破壊する現象のことです。
その名の通り、材料や部品を使用し始めてから遅れて破壊がやってくるため、遅れ破壊と呼ばれています。英語では「Delayed Fracture」と呼ばれます。
金属材料の破壊は普通、材料に急速な衝撃荷重が加わったときや、変動荷重によって疲労したときなどに起こります。
後者の破壊は「疲労破壊」と呼ばれており、金属材料の代表的な破壊現象として知られています。材料に繰り返し変動荷重が加わることで材料の弱い部分からき裂が発生し、き裂が広がることで起こります。
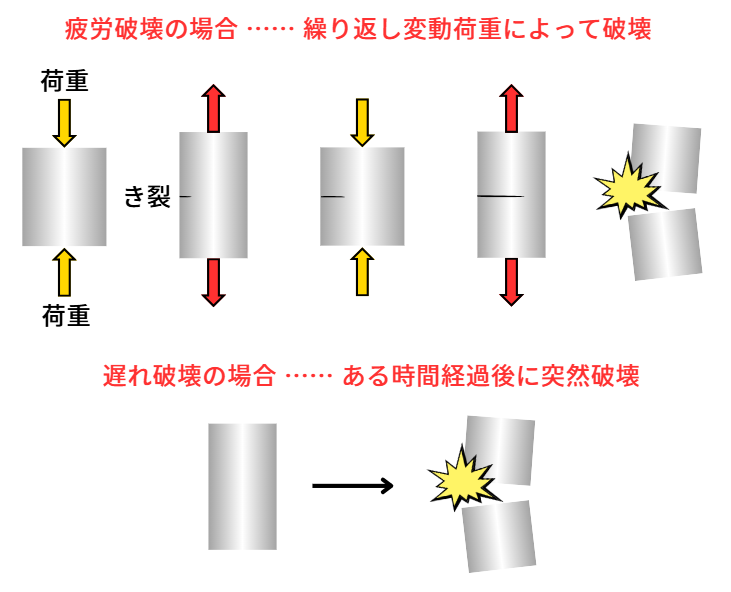
遅れ破壊と疲労破壊はどちらも時間が経ってから生じるため、似ている現象と言えます。
しかし大きな違いは、遅れ破壊は静的な負荷条件で生じるという点です。
材料に負荷している荷重が一定で変動性がないのに、材料がもろくなって突然破壊します。そのため、遅れ破壊は別名「静的疲労破壊」とも呼ばれています。
どんな部品で起こる?
遅れ破壊は、高強度鋼を使用した部品で起こりやすい現象です。
遅れ破壊が起こりやすい部品として有名なものが、橋梁や建築物において部材どうしを接合するために使用される高力ボルトです。
高力ボルトの遅れ破壊では、締め付け後、数か月~数年経ってから突然破壊します。ボルトの頭部首下やナットとの境界部などからポッキリと折れてしまいます。
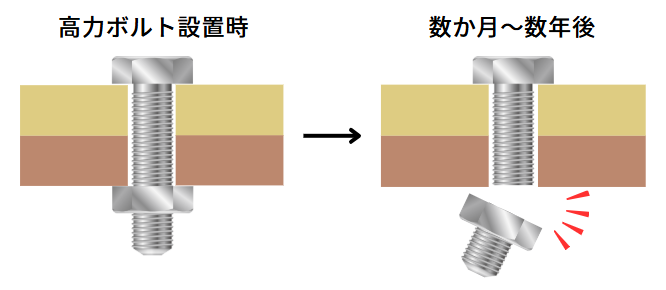
遅れ破壊を起こした箇所は、脆性(ぜいせい)的な破壊を生じています。
つまり、材料がガラスのようにもろくなって破壊したことを意味します。
また破壊を生じた箇所には、腐食した痕跡がよく見受けられます。
そのため、遅れ破壊は腐食によって生じるものと思われがちです。しかし、腐食は遅れ破壊の直接の原因ではありません。
のちほど詳しく解説しますが、腐食などによって生じた水素の侵入が深く関与しています。
過去には遅れ破壊が相次いだことにより、製造や使用が禁止となった高力ボルトもあります。遅れ破壊が原因でF13Tの製造が禁止となった話はあまりにも有名です。
F13Tは、かつて日本に存在した1,300MPa級の引張強さをもつ高力ボルトです。1964年にJISに制定されてほどなくして、橋梁に使用されたF13Tの遅れ破壊が相次いだことから製造禁止となりました。
1967年にはJISからF13Tが除外され、使用可能な高力ボルトの上限はF11T(1,100MPa級)となりました。しかし、F11Tにおいても同様の遅れ破壊が認められたことから、1979年のJIS改定時にはF11Tをなるべく使用しないよう明示されました。
現在は主にF10TやF8Tが使用されており、遅れ破壊は生じていません。しかし、F11Tが使用されたままの橋は全国に約7,000橋あると報告されており、対策が迫られています。
近年は、自動車用ハイテンにおいて遅れ破壊の発生が懸念されています。
ハイテンとは高い引張強さをもつ鋼板のことであり、薄くて軽いのに高い強度を誇ります。車体を軽量化できるため、燃費の向上とCO2の削減に効果的な材料として多くの自動車に採用されています。
いま自動車業界では、燃費の向上を図るためにハイテンの高強度化が進んでいます。1,500MPa級の超高強度のハイテンも登場しており、遅れ破壊の懸念も高まっています。
ハイテンについては以下の記事で詳しく解説していますので、ぜひあわせてご覧ください。
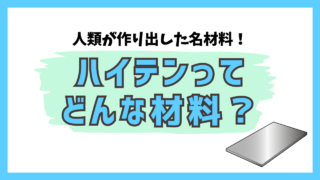
高力ボルトやハイテンに限らず、使用中に遅れ破壊が発生すると大きな事故につながりかねません。そのため、遅れ破壊が起こりやすい部品に対しては遅れ破壊対策を講じることが必要です。
知らなかったでは済まされない事態が起こらぬよう、高強度鋼を扱うエンジニアは遅れ破壊に対する知識を持っておくこと大切です。
遅れ破壊が起こる条件
一般的に遅れ破壊は、3つ要素が重なったときに起こるとされています。
3つの要素とは、「材料・応力・環境」です。これらの要素が相互的に作用することで遅れ破壊が起こります。
より具体的に言うと、次の3条件が当てはまるときに遅れ破壊が起こります。
詳しく見ていきましょう。
① 材料が高強度である
遅れ破壊は、材料の強度が高いものほど起こりやすいという特徴があります。
具体的には、引張強さが1,200MPa以上の鋼材において遅れ破壊の発生リスクが高まります。
下の図は、各種鋼材の引張強さと遅れ破壊の影響を示した図です。引張強さが1,200MPa程度までは遅れ破壊の影響が生じませんが、1,200MPaを超えると急激に遅れ破壊の影響が生じることが分かります。
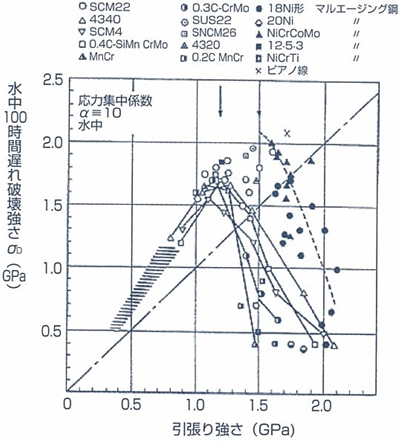
1,200MPa以上の引張強さをもつ鋼材には、焼入れを行ったクロムモリブデン鋼(SCM)、ニッケルクロムモリブデン鋼(SNCM)、マルエージング鋼などがあります。
また高強度の部類に入る部品としては、高力ボルト、PC鋼材、ハイテンなどが挙げられます。
② 材料に荷重が負荷している
遅れ破壊は、材料に荷重が負荷しているときに起こります。
運用中の機械や構造物では、材料には常に荷重が負荷しています。先ほど例を示した高力ボルトで見ると、高力ボルトは締め付け中に引張荷重が負荷しています。
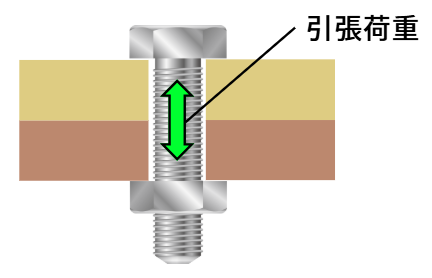
荷重が動的で変動性があるときは、材料は繰り返し荷重を受けることによって疲労し、疲労破壊します。一方の遅れ破壊は、荷重が一定状態の静的荷重のときに起こります。
また、通常時の破壊応力(引張強さ)よりもはるかに低い応力で破壊します。
③ 材料中に水素が存在する
遅れ破壊が起こる条件の中でもっとも特徴的と言えるのが、この「材料中に水素が存在すること」です。
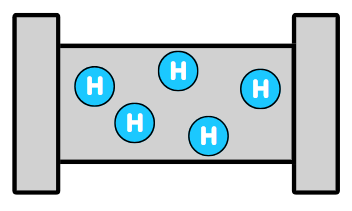
遅れ破壊の一番の原因は「水素」と言っても過言ではありません。
水素は材料の外部から侵入し、材料の内部にとどまります。内部に水素があると材料はもろくなり、そこに荷重が負荷すると遅れ破壊が生じます。
水素によって遅れ破壊が生じるメカニズムは、以下に詳しく解説します。
遅れ破壊の発生メカニズム
遅れ破壊は、材料内に侵入した水素が材料をもろくすることによって起こるとされています。
金属にとって水素はとてもやっかいな存在です。金属内にたやすく侵入して金属をもろくし、劣化させます。
水素が金属をもろくする現象は「水素脆化」と呼ばれ、金属材料界隈ではよく知られています。
水素脆化については以下の記事で詳しく解説していますので、ぜひあわせてご覧ください。
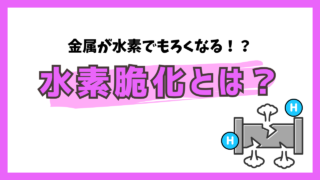
水素によって遅れ破壊が起こるメカニズムは、こうです。
①材料内に水素が侵入する
②水素が材料内で拡散し、応力集中部に濃化する
③応力集中部からき裂が生じ、進展する
このように、外部から侵入した水素が応力集中部に集まり、そこからき裂が発生・進展することで遅れ破壊が生じます。
ここで応力集中部とは、以下のような箇所が該当します。
ボルトでは頭部首下やねじ谷底が応力集中部となるため、き裂はたいていそこから生じて破壊します。
水素によってき裂が発生する理由は、水素が鉄同士の原子間結合力を低下させる、水素が局所的な塑性変形を促進するなど、学者によって色々な説が唱えられています。しかし、詳しいメカニズムはまだ解明されていません。
水素の侵入経路
ここまで読んで、「水素はいったいどこからやってくるの?」と疑問に思われたのではないでしょうか。
水素は、主に次の2つの経路で材料内に侵入します。
① 部品の製造工程で侵入する
1つ目は、部品の製造工程で水素が侵入するという経路です。
部品の製造時には、部品に対してさまざまな処理が行われることとなります。その中に水素の侵入が生じる処理があります。
代表的なものは、電気めっき処理です。
電気めっき処理は前処理工程を含めると、酸洗、電解脱脂、電気めっきの工程からなります。これらのいずれの工程においても水素が発生し、材料内に侵入します。
また、線材をボルトなどに圧造するさいに行われるりん酸亜鉛処理も水素侵入に影響をおよぼします。圧造後の熱処理時に材料が浸りんを起こし、遅れ破壊を助長させることが知られています。
このように、材料内に水素が侵入する可能性がある処理を行うさいは注意が必要です。
② 部品の使用中に侵入する
2つ目は、部品の使用中に水素が侵入するという経路です。
どうやって部品内に水素が侵入するかと言うと、主に腐食による侵入が挙げられます。
腐食とはいわゆる「サビ」のことですが、サビは金属に雨水がかかったときや、結露したときなどに生じます。
金属は腐食を起こすと、水素が発生します。そして発生した水素が材料の内部に侵入していきます。
そのため、雨水がかかりやすい場所や結露が発生しやすい場所などでは、遅れ破壊に注意が必要と言えます。
金属の腐食メカニズムについては次の記事で詳しく解説していますので、ぜひあわせてご覧ください。
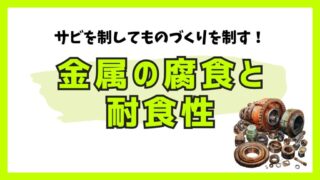
遅れ破壊の対策
高強度鋼の遅れ破壊を防止するには、どのような対策が有効となるのでしょうか。
ポイントとなる対策方法は、以下の通りです。
詳しく見ていきましょう。
① 製造時の水素の侵入を阻止する
遅れ破壊をもたらす主犯格は水素であるため、製造中の水素の侵入を阻止することが遅れ破壊対策に有効です。
電気めっき処理を行うときは、水素の侵入量をおさえるためにできるかぎり処理の時間を短くします。
電気めっき処理を行ったあとは、ベーキング処理を行います。ベーキング処理とは、材料中に侵入・拡散してしまった水素を除去するための熱処理のことです。部品を190~230℃の温度で4時間以上加熱します。
りん酸亜鉛被膜処理を行ったときは、熱処理前にりん酸亜鉛を除去します。もしくは、りんを含まない被膜剤を使用することで遅れ破壊の発生リスクを低減できます。
② 使用時の水素の侵入を阻止する
使用時に生じる部品の腐食は、水素の侵入をもたらします。そのため、使用時の腐食を防止することが遅れ破壊対策に有効です。
部品に結露が発生しないように通気をよくし、また、雨水などがかからないような構造とします。
表面塗装による防錆処理や、防水コーティングなどを行うことも水素侵入対策に有効です。
③ 応力集中を阻止する
遅れ破壊は応力集中部から生じるため、一箇所に応力が集中しない部品形状とすることが遅れ破壊対策に有効です。
例えば高力ボルトでは、頭部首下やねじ谷底に大きなアールを取り、応力集中しないようにします。
また、穴や切り欠きが生じない形状とすることも有効です。
④ 耐水素脆化特性が優れた材料を使用する
材料メーカーでは、耐水素脆化特性に優れた材料の開発が精力的に行われています。そのような材料を使用することが遅れ破壊対策に有効と言えます。
材料の耐水素脆化特性を確保するため、以下のような対策が取られています。
これらの対策により、高強度鋼において侵入した水素を無害化することが可能となってきました。
メーカーの努力もあり、今では14T(1,400MPa級)の超高力ボルトが開発され、実際に使用されています。現在、18T(1,800MPa級)の高力ボルトの開発も進められています。
おわりに
本記事では、高強度鋼の遅れ破壊について解説してきました。
金属材料の構造や特性にかかわる話であったため、ちょっと理解しづらいと感じた方もいると思います。
ただ、ものづくりではこのように金属材料の知識が必要となる場面が多くあります。
もっと根本的に金属材料の勉強をしたいという方のために、おすすすめの書籍を紹介しておきます。ぜひ参考になさってください。
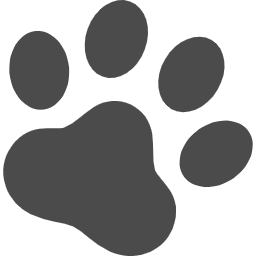